地址:海南省海口市秀英区西秀镇华煌科技工业园71号 联系电话:153-3898-9511
copyright © 2017 海南中德晶石新型建材有限公司 版权所有 琼ICP备17004453号-1
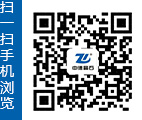
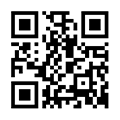
电话:153-3898-9511
地址:海南省海口市秀英区西秀镇华煌科技工业园71号
海南空心微珠轻质陶粒的制备与性能
来源:中德晶石 发布时间:2021-07-05 11:15:41 浏览次数:88
空心微珠轻质陶粒的制备与性能
摘要:以煤矸石空心微珠和玻璃空心微珠坯体为主要原料,采用滚动成球法制备陶粒生坯,经烘干、烧结,得到轻质陶粒,研究了烧结温度、保温时间以及玻璃粉添加量对空心微珠轻质陶粒性能的影响。结果表明:随着烧结温度的升高,陶粒的表观密度和吸水率逐渐增大,颗粒抗压强度先增大后逐渐减小;烧结温度为700℃,单颗粒抗压强度为200.5N,达到最大值。随着保温时间的延长,颗粒抗压强度先增大后减小。加入玻璃粉可以明显提高陶粒的单颗粒抗压强度,并且随着玻璃粉加入量的增大,颗粒抗压强度显著增大,700℃烧结的样品中玻璃粉加入量为25%(质量分数)时,单颗粒抗压强度增大到327.5N,提高了63.3%。
关键词:煤矸石空心微珠;玻璃空心微珠;表观密度;颗粒抗压强度
陶粒是我国近几年发展较快的建筑材料之一,目前陶粒的生产方法主要有破碎法和成球法[1]。破碎法是将原料直接破碎、烧结制得陶粒;成球法是将原料粉碎、成球、烧结制得陶粒。但是,无论哪种方法制备陶粒,其烧结温度都比较高,多数高于1000℃。
煤矸石是我国排放量最大的工业固体废弃物之一,每年的排放量相当于当年煤炭产量的10%左右,达(1.2~1.6)×1011kg,现已累计堆存约5×1012kg[2]。
煤矸石的堆放占用大量的土地面积,同时使得周围的耕地变得贫瘠,不能被利用。煤矸石除含有SiO2、、Fe等常见元素外,还有Pb、Sn、As、等其他微量重金属元素,这些元素为有毒重金属元素,严重危害水土[3–5]。同时,我国玻璃制品的用量也逐年增大,不可避免地产生了大量废弃玻璃。我国每年城市的废弃玻璃约(4.0~7.5)×109kg,占城市生活垃圾总量的3%~5%[6]。玻璃的化学性质稳定,很难分解。
以煤矸石和废弃玻璃为原料生产陶粒,用于建筑材料以及污水处理领域,既可以大量消耗煤矸石和废玻璃又能改善环境。李虎杰等[7]将煤矸石经破碎、粉磨,与添加剂混合成球,在烧结温度为℃条件下制得的陶粒堆积密度为723kg/m3。
陈彦文等[8]以煤矸石为主要原料,在烧结温度为℃条件下制得的陶粒堆积密度为758kg/m3。
杨稔等[9]利用煤泥、粉煤灰和煤矸石在烧结温度为℃条件下制得的陶粒吸水率为63.5%,表观密度为900kg/m3。程伟[10]以废弃玻璃和粉煤灰为原料,在烧结温度为1140℃条件下制得的陶粒表观密度为1150kg/m3。由此可见,目前制备陶粒的烧结温度大多都在1000℃以上,所得陶粒的表观密度均不低于700kg/m3。
空心微珠是一种新型的基础工业原料,本课题组研究了空心微珠对氧化铝陶瓷性能的影响[11–15],等[16]和Zhang等[17]以聚空心微珠作为成孔剂制备氮化硅多孔陶瓷,另外,侯博智等[18]利用粉煤灰空心微珠制备多孔陶瓷,吕瑞芳等[19]利用煤矸石空心微珠坯体制备多孔材料。玻璃空心微珠坯体有很好的烧胀特性[20],Qu等[21]利用玻璃空心微珠堆烧制备出轻质高强的新型泡沫玻璃。
目前,国内外对于利用空心微珠制备陶粒的报道较少,而且关于陶粒的膨胀机理,文献[22–25]认为主要是靠原料中的Fe2O3在1100℃以上的高温下发生一系列氧化还原反应,释放大量的气体,从而使陶粒膨胀。
利用玻璃空心微珠的烧胀特性与煤矸石空心微珠混合成球,在较低的温度下制备表观密度小于的轻质陶粒。
陶粒生坯形貌陶粒生坯是由煤矸石空心微珠和玻璃空心微珠坯体及玻璃粉构成的平均粒径为10mm的球体,陶粒生坯的宏观照片如图5所示。由图5可以看出,陶粒生坯粒径分布均匀,颗粒大小基本一致。
图5空心微珠陶粒生坯的宏观照片图6a为不含玻璃粉的陶粒生坯微观形貌照片。由图6a可以看出:煤矸石空心微珠和玻璃空心微珠坯体均匀地分布在陶粒生坯内部,两者均保持完整的圆球形,表面相对光滑的为玻璃空心微珠坯体,表面相对粗糙的为煤矸石空心微珠,陶粒生坯内部微珠之间存在大量的空隙;添加玻璃粉后,微珠之间的空隙中出现玻璃粉颗粒,如图6b所示,煤矸石空心微珠和玻璃空心微珠坯体之间的空隙逐渐被玻璃粉填充,使陶粒生坯变得密实。
烧结温度对陶粒性能及物相的影响
为没有添加玻璃粉陶粒生坯烧结后吸水率、表观密度和抗压强度随烧结温度变化曲线,保温时间是60min。
由图7可以看出:随着烧结温度的升高,空心微珠陶粒的吸水率和表观密度逐渐增加,颗粒抗压强度先增大后减小。
图8为空心微珠陶粒生坯经不同温度烧结后的微观形貌SEM照片。由图8可以看出,随着烧结温度的升高,玻璃空心微珠坯体的微观形貌发生显著变化,实验所用煤矸石空心微珠经过高温烧结,因此在陶粒烧结过程中不会发生显著变化。600℃烧结后,玻璃空心微珠坯体表面开始玻化、变得粗糙,形状出现不规则现象,并伴有微膨胀,如图8a所示,这是由于玻璃粉在此温度下开始出现软化现象引起的;烧结温度升高后,部分玻璃空心微珠坯体开始出现膨胀破裂现象,随着温度继续升高,出现破裂的玻璃空心微珠坯体数量增加,破裂开口的尺寸也越大,当烧结温度升高到1100℃后,如图8d所示,玻璃空心微珠坯体完全软化,流动性增大,熔融的玻璃相包覆并填充在煤矸石空心微珠的间隙中。
图6陶粒生坯的SEM照片空心微珠陶粒的吸水率取决于煤矸石空心微珠、玻璃空心微珠以及两者形成的空隙,600℃烧结后的样品中,玻璃空心微珠形成基本封闭的球体,吸水率极低,随着烧结温度的升高,玻璃空心微珠逐渐膨胀破裂,样品内部的开孔及连通孔增加,导致吸水率逐渐上升。
烧结温度为600℃时,样品吸水率最低为,表观密度最小为595.0kg/m3。随着烧结温度的升高,玻璃空心微珠逐渐膨胀破裂,开孔增多,样品吸水率增大的同时,表观密度增大,700℃时,吸水率56.9%,表观密度增大到653.1kg/m3,1000℃和1100℃时,吸水率分别为71.4%和81.2%,表观密度分别增大到651.8和733.2kg/m3。
烧结过程陶粒的强度主要取决于玻璃空心微珠之间的结合以及玻璃空心微珠与煤矸石空心微珠之间的结合,600℃烧结后的样品中,玻璃空心微珠刚刚出现软化现象,黏结力较弱,抗压强度较低,仅有79.7N。当烧结温度升高到700℃,样品中玻璃空心微珠软化加剧并且膨胀粘连,使其与煤矸石空心微珠之间的结合力大大增加,强度迅速上升到。随着烧结温度的进一步升高,玻璃空心微珠膨胀加剧,破裂口增多、尺寸增大,从而降低了样品的抗压强度,当烧结温度为1100℃时,样品内部的孔结构塌陷,如图8d所示,抗压强度降低至91.9N。
烧结温度对陶粒物相的影响
图9为陶粒生坯的TG–DSC曲线,200℃之前陶粒失去自由水,质量减少4%;200~600℃之间,陶粒失去结合水和成球时喷洒的PVA,质量减少3.7%;600~1100℃,质量减少0.9%,这由于陶粒高温下物相转变而产生微量气体。不同烧结温度陶粒样品的XRD谱见图。对比图4可知,煤矸石空心微珠中的莫来石和α-石英(α-Quartz)的特征峰在陶粒烧到℃时开始减弱,方石英和钙长石的特征峰均有所增强,说明玻璃空心微珠坯体提供大量的SiO2以及Na2O等矿化剂,促使方石英析晶,因此烧结温度为600℃时,方石英晶体持续析出[27–29],莫来石转化为钙长石。700℃时开始出现1个强度较弱的霞石衍射峰,800℃时莫来石特征峰基本消失,霞石和钙长石的特征峰增强,烧结温度为1100℃时,霞石特征峰完全消失,呈现出钠长石特征峰,表明霞石转化为钠长石。
保温时间对陶粒性能的影响
图11为没有添加玻璃粉的陶粒生坯烧结后吸水率、表观密度和抗压强度随保温时间的变化曲线,烧结温度为700℃。由图11可以看出,随着保温时间的延长,陶粒的吸水率和逐渐增加,抗压强度先增大后减小。
玻璃空心微珠已经出现膨胀和少量破裂现象,随着保温时间的变化,这种膨胀破裂的现象逐渐增加。
保温时间为30min时,分别为45.0%和玻璃空心微珠的熔融程度不够,黏度还比较大[30],样品中出现破裂的玻璃空心微珠较少,吸水率和表观密度较低,分别为45.0%和628.9kg/m3,随着保温时间的延长,破裂现象增加,引起吸水率和表观密度上升,保温时间为150min时,陶粒的吸水率和表观密度分别为62.1%和666.7kg/m3。
结合图11c可知,700℃烧结后的样品抗压强度均保持较高水平,随着保温时间的延长,抗压强度的变化先出现小幅上升,然后缓慢下降,当保温时间为30min时,陶粒的颗粒抗压强度为183.8N,时增大到200.5N,150min时又减小到171.2N。
这是由于在烧结过程中,玻璃空心微珠逐渐软化,一方面增加相互之间以及煤矸石空心微珠之间的结合力,有利于增强抗压强度;另一方面,玻璃空心微珠膨胀破裂现象逐渐增多,影响强度。当保温时间小于60min时,结合力的增大作用大于微珠破裂的破坏作用,表现为样品的抗压强度增大,当保温时间超过60min后,微珠破裂现象占主导地位,引起样品的抗压强度缓慢下降。
外掺玻璃粉对陶粒性能的影响
图13为外掺玻璃粉空心微珠陶粒样品的吸水率和抗压强度随玻璃粉加入量的变化曲线。由图可以看出:烧结温度为700℃时,没有掺加玻璃粉的样品吸水率为56.9%,玻璃粉加入量为5%的样品吸水率减小到46.0%;随着玻璃粉加入量的增加,样品的吸水率进一步减小。烧结温度为800和900℃时,样品的吸水率随玻璃粉加入量的变化趋势与℃时基本一致。由图13b可以看出:随着玻璃粉加入量的增加,3个烧结温度烧结的样品抗压强度均逐渐增大。烧结温度为700℃时,没有掺加玻璃粉的样品抗压强度为200.5N,玻璃粉加入量为5%时,样品抗压强度增大到210.7N,玻璃粉加入量增大到时,抗压强度增大到327.5N,提高了63.3%。
表2为相关文献中陶粒表观密度和颗粒强度。
由表2可以看出,本方法制备的陶粒能够实现低温烧结制备高强度、低密度的陶粒。
图14为烧结温度为700℃、玻璃粉加入量为时陶粒样品的微观形貌SEM照片。由图14可以看出,与没有添加玻璃粉的样品相比,内部出现大量微孔,同时有较多断开的煤矸石空心微珠存在。
由图6b可知,生坯中添加的玻璃粉分布在空心微珠形成的空隙中,在烧结过程中玻璃逐渐软化,连接到一起将颗粒空隙中的气体包裹其中形成大量微孔;同时软化的玻璃粉颗粒增加煤矸石空心微珠彼此之间的结合力,使得样品由沿球断裂变为穿球断裂,显著提高了样品的抗压强度[36]。
结论
随着烧结温度的升高,陶粒的表观密度和吸水率均逐渐增大,颗粒强度先升高后降低,700℃时,颗粒抗压强度达到最大值200.5N。
随着烧结温度的升高,α-石英和莫来石相转变为方石英和钙长石,800℃时开始析出霞石,℃霞石又转变为钠长石。
烧结温度700℃时,改变保温时间,颗粒强度先增大后减小,当保温时间为60min时,颗粒抗压强度为200.5N,达到最大值。
加入玻璃粉可以增强煤矸石空心微珠之间的粘结力,显著改善陶粒颗粒强度,玻璃粉加入量为25%时,陶粒的强度提高63.3%。
上一篇: 海南膨胀珍珠岩自动填充方式的几大优势
下一篇: 海南高性能水泥基陶粒吸音材料的研制